Solutions for the energy recovery industry
The ABC&I deNOx-technology is creating a chemical reaction taking the NOx away from the flue gas. The upper part of the free fire place volume in the boiler is used. This section is utilised as an internal "chemical reactor" volume for the deNOx -reaction. Reaction kinetics and efficiency is controlled by the ABC&I deNOx -technology. Used chemicals are nitrogen based.
NOx -reduction in the various types of boiler systems used in the energy recovery industry are complex. Requirements are demanding not only on reduction in NOx but also in respect to added chemical-slipp to the flue gas together with elimination of the potential risk of enhanced CO-emissions as well as inter activated formation of N2O.
ABC&I´s products in the field of NOx -reduction are based on chemical NOx -reduction by means of a nitrogen based reduction agent e.g. ammonia, or carbamide.The reaction takes place at temperatures at ca 900 ºC, depending on physical and chemical conditions.
Environmental benefits
Lessened NOx-emissions to atmosphere are lowering negative impacts on the receiving eco system. The most pronounced are:
- Acid rain
- Ozone formation on ground level ie aggressive smog formation
- Nitrogen outlet to the marine eco system
- Lower NOx -emissions reduces the negative influence to humans as well as to other living species
NOx-formation in the combustion zone of the boiler
NOx sources are:
a. Thermal NOx-dominating at high temperatures in the combustion zone
b. Fuel nitrogen NOx - stemming from the nitrogen content in the fuel
c. Prompt NOx - formed by radicalized hyrocarbon fractions and nitrogen/oxygen
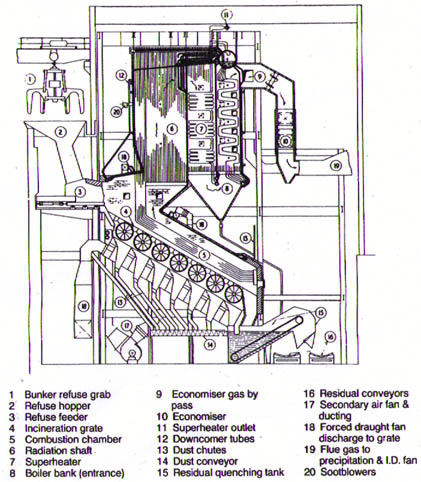
Design adapted to combustional conditions
The installed deNOx-system must be specific designed to the individual boiler.
The deNOx-system function must be able to adapt to the existent conditions in the boiler. Design of equipments, advanced construction materials and intelligent control software is crucial for the system performance. Important boiler characteristics are: flame pattern temperatures, oxygen potential in oxidizing zones, retention time and gas flow patterns.
Gas temperatures in the flame zones of the burners/fuel bed on the grate are normally 1200ºC - 2000ºC. In order to accomplish a full combustional oxidization of carbon/hydrocarbon fractions from solid fuels, temperature needs to exceed temperatures in the interwall of 800ºC - 900ºC as a typical case. Long enough gas retention time above these temperatures are also of essential importance.
Used deNOx chemicals
The most potent reduction agents for the NOx-reduction are normally nitrogen based. For best performance the most appropriate chemical shouldbe used. The selected chemical for for NOx-reduction should satisfy varrious types of criteria. Criteria which will be different depending on the specific operational conditions in the combustional zones of the boiler. ABC&I provides deNOx- reduction options in respect to all commercial available reduction agents. Based on the boiler design, the most appropriate reduction agent is selected.
ABC&I have vast experience from excisting reference plants where selected chemicals have shown to produce the most optimal results in different types of fuel/boiler systems.
Investment costs- Non catalytic NOx-reduction
Investment costs are comparatively low in respect to other measures against emissions such as technologies based on catalysis or scrubber absorption.
Chemical costs
Cost of chemicals is an important factor in reducing NOx-emissions. Selecting the best technology design is much a question of chemical use efficiency. A low technology based NOx-reduction could require twice the quantity of the chemicals at a specific NOx-emission level. A high added chemical slipp emission is usally also a connected problem.
Potential impact on the energy producing boiler
Used reduction agents are potent chemicals and must be treated in accordance with normal chemical processing procedures.
The equipments used in the NOx-reductionsystem must have high enough standard in respect to chemical exposure, destructive forces from high temperatures (ca 1000ºC) and a corrosive flue gas with in some cases sticking prone components. The NOx-reducing equipments must also resist the aggressive environment after many years of operation, giving a safe and reliable operation in respect to NOx-reduction and to the energy production in the boiler itself.
The most appropriate technical design for NOx-reduction is selected depending on type of fuel/boiler system and requirements on NOx, NH3-slipp, operational costs etc. Several and different types of deNOx projects delivered to the energy recovery industry make the ABC&I company to a leading supplier in this highly specialized field.
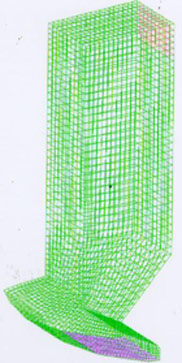
CFD-based boiler analysis
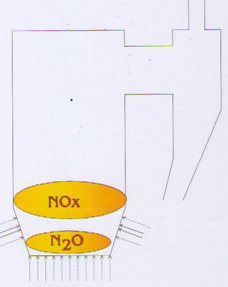
Emission generating bed zones in a CFB-boiler
|